HAT-320 Compressed Air Filling Pump
The HAT-320 series high-pressure air compressor (automatic intelligent) is a three-stage, three-cylinder compressor, featuring a W-type piston layout for three-stage compression of air with air cooling.
Keyword:
Classification:
Filling Pump Series
Overview of HAT-320 High Pressure Compressor (Automatic Intelligent)
The HAT-320 series high pressure air compressor (automatic intelligent) is a three-stage three-cylinder compressor, designed with a W-type piston layout for three-stage compression of air cooled. It compresses air from a free state to a maximum of 30MPa, and after passing through the oil-water separator and purification filter in the unit, it removes water, oil, and impurities contained in the high-pressure gas, ensuring that the output high-pressure gas is clean and odorless, making it a reliable and safe source of breathing air.
The features of this unit include patented valve plate assemblies for the first and second stage intake valves; multi-cylinder multi-stage compression with coolers installed at each stage, ensuring reasonable piston force distribution; the oil pump lubrication can promptly meet the lubrication and cooling needs of all components and plunger parts; excellent lubrication and cooling effects, low noise, using patented noise air filters and low noise valve assemblies; the final stage cylinder sleeve is made from a proprietary patented formula, with alloy materials that are wear-resistant, have a small thermal expansion coefficient, and are easy to assemble and disassemble.
This unit is equipped with a motor overload device to ensure operation within the set pressure range, guaranteeing the safety of operators and the unit, with a continuously adjustable safety valve serving as the last safety barrier for the unit. The unit has a simple structure, is easy to maintain, operates at low speed, produces low noise, and is of high quality, safe, and reliable. The air quality meets the national standard GB18435-2007 "Standard for Breathing Gas for Diving" and complies with the European standard EN12021 "International Standard for Breathing Compressed Air."
The HAT-320 high pressure air compressor (automatic intelligent) features high performance, reliability, durability, and economy, making it the preferred product for a wide range of users both domestically and internationally. It is widely applicable in emergency rescue, firefighting, diving, marine engineering, petrochemicals, shipping, national defense, sports, precision instruments, gas tightness testing, laboratories, and small factory gas supply.
HAT-320 High Pressure Compressor (German Version) Parameters
Serial Number | 12 | 13 |
Model | HAT-320 | BW320SH |
Drive | 380V Three-Phase Motor | GX390 Gasoline Engine |
Power KW | 7.5 | 12HP |
Main Engine Speed r/min | 1440 | 1440 |
Protection Level IP | IP55 | / |
Net Weight Kg | 170 | 168 |
Displacement L/min | 320 | |
Working Medium | Air | |
Working Pressure Mpa | 20-30 | |
Compressor Stages | Three-stage Compression | |
Oil Tank Capacity L | 2.8 | |
Lubricating Oil Model | BS750 (Food Grade Special Oil) | |
Noise dB | ≤78 | |
Dimensions mm | 1100×580×670 | 1220×580×670 |
Oil/Water Separation | Final Stage Oil-Water Separator | |
Final Stage Filter Group | Activated Carbon, Molecular Sieve, Alumina Purification Filter | |
Air Quality | Meets the national standard GB18435-2007 "Standard for Breathing Gas for Diving" and complies with the European standard EN12021 "International Standard for Breathing Compressed Air." | |
Remarks | Optional or Customizable |
Equipment Operating Environment
The air compressor should be placed in a clean and ventilated area, equipped with a qualified power supply system. To ensure gas quality, the location should not contain exhaust gases, harmful gases, or excessive dust, and should not have any explosion or fire hazards. The compressor should not be tilted more than 15 degrees from the horizontal plane, and sufficient space should be left around the compressor for heat dissipation and operation.
![]() | ![]() |
Preparation Before Starting
Check the lubricating oil level of the equipment. Note: Both high and low oil levels are considered abnormal operating conditions for this equipment. If the oil level exceeds the upper mark, it is too high, which is detrimental to heat dissipation and can easily cause carbon buildup on the gas valves, leading to negative pressure oil spitting; if the oil level is below the lower mark, it will cause poor lubrication, leading to insufficient oil at lubrication points, accelerating component wear, and even causing cylinder seizure or shaft breakage. The lubricating oil selected for this equipment is HL-N150 special oil produced by Haiant. Check the circuit wiring. 1. Connect the power line correctly according to the circuit wiring diagram, and reliably connect the ground wire. Check the grounding resistance value according to the protection or operation requirements of the compressor power system. 2. Check the data on the compressor ID plate for compatibility with the power supply, especially the rated current and rated voltage. 3. Start (jog) the compressor to check the rotation direction; the correct direction should cause the strong airflow generated by the fan to blow towards the cylinder. If the motor rotation is incorrect, swap any two phases (A, B, C) of the three-phase input. 4. The cross-section of the external power supply line for the three-phase motor plug of this equipment should not be less than 4m2 copper core cable, with a length of less than 6m. A long line can increase resistance, reduce voltage, accelerate motor heating, and may even prevent startup; the machine must be reliably grounded. | ![]() |
Manual Shutdown Circuit Diagram
Automatic Shutdown Circuit Diagram
Check the V-belt
1. Check the tension of the V-belt and the connection status of each part (when the power is off).
2. Manually rotate the main engine fan to see if it operates normally.
Check the high-pressure hose
1. Check the high-pressure hose to ensure there are no creases, no air holes, damage, or leaks.
2. Check if there is any leakage when connecting the high-pressure hose to the equipment exhaust joint.
Starting and Stopping
1. Before starting the equipment, first open the various drain valves to release the residual gas inside the equipment, then close the drain valves. Starting with no load can extend the service life of the equipment.
2. Press the start button.
3. Press the stop button.
Important: Taking a three-phase motor as an example, check whether the rotation direction of the motor is consistent with the direction indicated by the arrow on the protective cover.
Important: These operations must be performed by personnel who have qualified training in compressor use; please read the attached product manual carefully before starting the compressor.
High-Pressure Safety Valve and Pressure Sensor
1. The high-pressure safety valve of the compressor is set with a final safety valve trip value at the factory. When the pressure of the compressor reaches this value, the safety valve will automatically release pressure, and the safety valve will close when the pressure is below the set value.
2. Pressure sensor, which gives a signal when the pressure reaches the set value, causing the equipment to stop automatically.
Warning:
1. It is strictly prohibited to disconnect the hose from the equipment or from the inflation switch when the compressor is compressing gas.
2. According to national regulations, each level of safety valve should be calibrated annually.
Notes for Trial Operation
1. Press the start button.
2. Observe whether the pressure gauge data is normal.
3. Observe whether the equipment is operating normally.
Notes for Filling Operation
1. Connect the high-pressure hose to the gas cylinder.
a. Choose a certified high-pressure cylinder, and the maximum filling pressure must not exceed the safe working pressure of the cylinder.
b. Check that the high-pressure filling hose has no scars or leaks.
c. Connect the filling hose to the cylinder that needs to be filled and open the valve on the cylinder.
2. When starting the compressor with no load, a knocking sound for about three seconds is a normal phenomenon indicating that the last stage cylinder is starting to work.
3. Start the compressor, and after it stabilizes, fill the cylinder with gas. Check the pressure gauge for any abnormal changes; if there are any, stop and check.
4. When the filling pressure reaches the preset value, the machine will stop automatically; please close the valve on the cylinder.
5. The equipment needs to drain once every 20-30 minutes to discharge filtered moisture and impurities.
6. After the high-pressure air in the filling hose is released, remove the filled cylinder.
7. Due to the presence of a pressure maintenance valve set at 10-15Mpa, the last stage pressure gauge will not display for about one minute after the machine starts. It is normal for the pressure gauge to start displaying after the pressure reaches 10-15Mpa.
Note:
A: The filling cylinder is less than 12L.
B: Do not operate at full load for extended periods; long-term full-load operation will reduce the service life of the equipment.
C: In case of an emergency during the filling process, ① sudden power failure; ② motor shutdown due to overload; ③ sudden inability to operate; use the main power switch to completely stop the compressor and promptly close the cylinder valve.
D: After the filling operation is completed, the internal air pressure of the equipment must be released to prevent the equipment from starting under load again, which affects the machine's service life.
Daily Maintenance of Equipment
Item | Content | Check or Replace Cycle (h) Hours | Remarks | ||||
Every operation | 50 | 100 | 200 | 1000 | |||
Air Filter element | Remove surface dust Impurities | * | The visible ash content condition can be extended or shortened. | ||||
Replace with a new filter element | * | ||||||
Belt | Check, adjust | * | Belt drive type | ||||
Replace | * | ||||||
Oil level check | Is it sufficient? | * | Replace after the first operation of 50 hours, then replace every 200 hours thereafter. | ||||
Replace | * | ||||||
Last stage Filter element | Replace | * | Ensure gas quality | ||||
Last stage air filter drainage | Is drainage performed? | * | Drain once every 20-30 minutes. | ||||
Oil-water drain valve drainage | Is drainage performed? | * | Drain once every 20-30 minutes. | ||||
Automatic shutdown device | Is it normal? | * | If it cannot automatically shut down, please check. | ||||
High-pressure inflation valve | Is there any leakage? | * | If there is a leak, please replace. | ||||
High-pressure pressure gauge | Is there any oil leakage? | * | If there is a leak, please replace. | ||||
Check the high-pressure filling hose. | Are there any creases, air holes, damage, or leaks? | * | If damaged, please replace. | ||||
Various levels of safety valves. | Inspection. | * | Calibrate once a year according to national regulations. |
Note: * indicates maintenance cycle.
Equipment fault elimination.
If abnormalities occur after the compressor is started, the cause must be identified immediately, and the fault must be eliminated before restarting.
Equipment fault elimination reference table.
Fault phenomenon. | Possible causes. | Elimination methods and countermeasures. |
Compressor cannot start. | 1. Poor contact of the start button. | Repair or replace equipment by electrical and equipment personnel. |
2. Poor circuit contact. | ||
3. Voltage too low. | ||
4. Power supply phase loss. | ||
5. Motor failure. | ||
6. Main unit failure. | ||
High operating current, compressor automatically shuts down. | 1. Voltage too low. | 1. Check and adjust by electrical and equipment personnel. |
2. Exhaust pressure too high. | 2. Check and adjust pressure parameter values correctly. | |
3. Compressor main unit failure. | 3. Repair and eliminate by electrical and equipment personnel. | |
Compressor cannot achieve set working pressure. | 1. Drain valve leaking, pipeline leakage. | 1. Reseal and tighten. |
2. Final stage pressure safety valve damaged. | 2. Adjust or replace safety valve. | |
3. Wear of final stage piston part gaps. | 3. Replace piston parts. | |
4. Pipeline joints loose. | 4. Retighten joints. | |
Compressor overheating. | 1. Fan rotation direction incorrect. | 1. Correct it. |
2. Poor cooling. | 2. Remove dust from various cooling pipes and cylinders. | |
3. Ambient temperature too high. | 3. Choose a cool place to stop and cool down. | |
4. Long-term overload operation. | 4. Reduce load. | |
Safety valve leakage. | 1. Long service life of safety valve, spring fatigue. | 1. Replace. |
2. Pressure control failure, working pressure too high. | 2. Partial repair by qualified personnel. | |
3. Seal failure. | ||
Discharged gas has an odor or oil smell. | 1. Purifier filter material saturated or not drained in time. | 1. Replace filter element, add oil according to manual standards, and drain in time. |
2. Used unqualified lubricating oil. | 2. Replace with specified lubricating oil. | |
3. Severe wear of piston rings. | 3. Replace worn parts. |
Methods to extend compressor life.
1. Ensure a clean working environment.
2. Replace special lubricating oil as required or in advance.
3. Drain in time.
4. Lower machine temperature.
5. Arrange maintenance work as necessary.
Contact Us
Service Phone:
Contact E-mail:
Contact Address:
100 meters south of Chengnan Chenzhuang Junction, National Highway 220, Changqing District, Jinan City, Shandong Province
What makes us so different from other suppliers?
The company is committed to the research and development and production of personal protective equipment for emergency rescue, and at the same time supporting the sales service and training of related safety protection equipment and equipment.
Strong Strength
Shandong Haiante company was founded in 2003, covers an area of 15,000 square meters, more than 30 professional R & D technicians, 3 senior engineers.
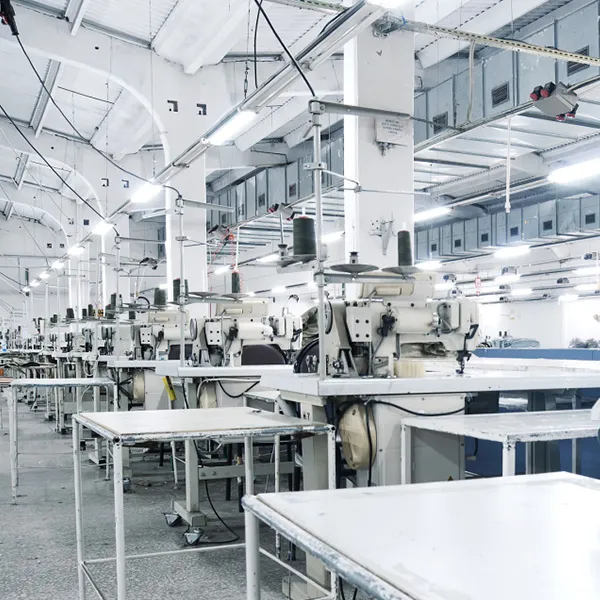
Qualification
The products have obtained the special product production license issued by the quality supervision department and passed the type inspection and some certifications of the National Fire Equipment Quality Center.
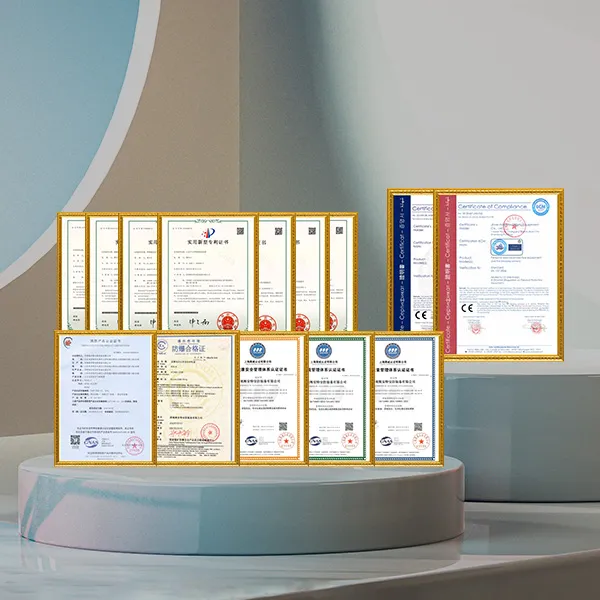
After-sales Service
The products cover 26 provinces, more than 500 cities, and more than 10 surrounding countries, providing personal protective equipment support for more than 20000 workers across the country every year
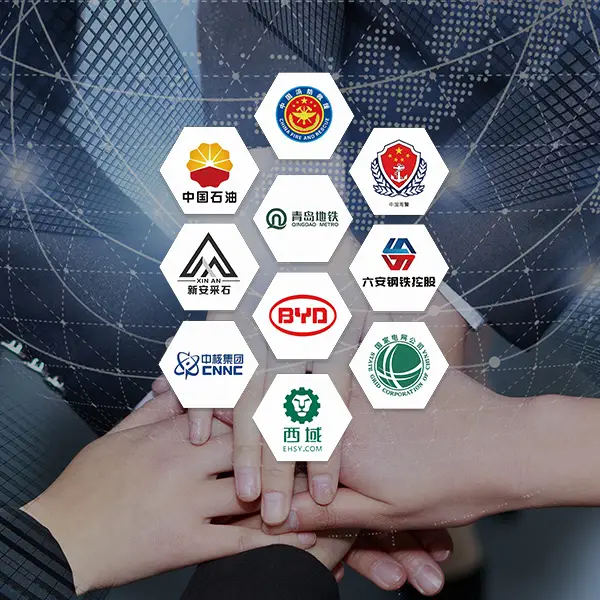
After-sales Service
We provide timely, complete and comprehensive pre-sales, in-sales, after-sales, and services for all Hyant users, so that products and services follow each other, and continuously improve the overall service quality of the company is our service goal.
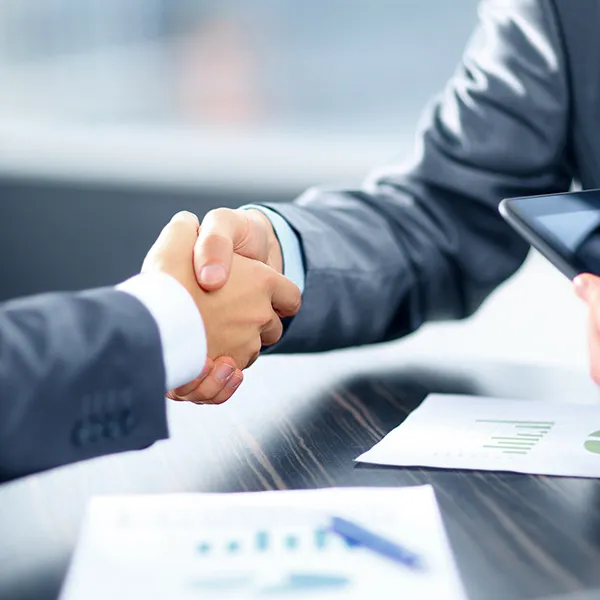
Need help? We're here to help!
Please contact us to provide you with satisfactory products and become a reliable supplier and service provider in the industry.
Other Products
Occupational safety and health special protective equipment, fire emergency rescue individual protective equipment
Isolated Positive Pressure Oxygen Breathing Apparatus (Cabin Type)
Positive pressure oxygen respirator (bag type)
Positive pressure fire-fighting oxygen respirator
Oxygen respirator packaging box